La corrosion des armatures dans le béton : Un défi structurel
La corrosion des armatures dans le béton est un problème majeur qui menace la durabilité des structures. Dans cet article, nous explorerons les mécanismes de corrosion, ses causes et ses conséquences, ainsi que les mesures préventives disponibles pour assurer l’intégrité des ouvrages en béton armé et précontraint.
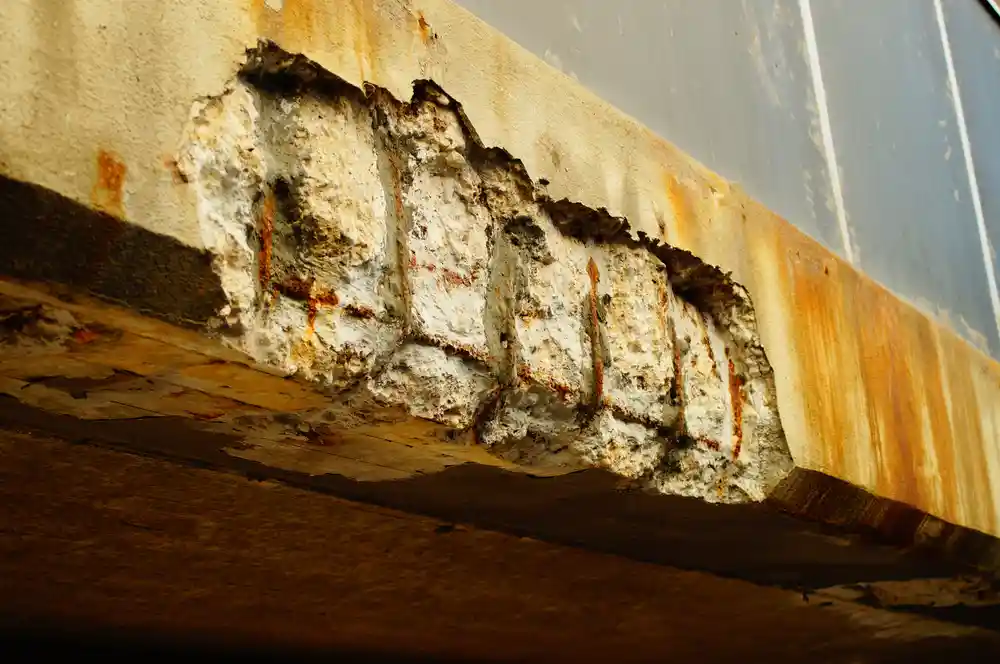
Qu’est ce que la corrosion dans le béton armé ou précontraint ?
La corrosion dans le béton armé ou précontraint est un phénomène qui survient lorsque l’environnement autour des armatures métalliques rompt l’équilibre protecteur naturellement formé par le béton.
En effet, en raison de sa basicité, avec un pH d’environ 13, le béton sain crée un environnement naturellement protecteur pour les armatures, formant ainsi un film passif (solution solide Fe3O4 – Fe2O3) qui ralentit considérablement la vitesse de corrosion.
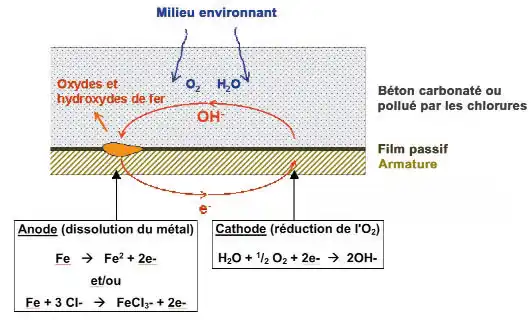
Cependant, dans certaines conditions telles que la carbonatation du béton d’enrobage ou une concentration critique en chlorures, cet équilibre protecteur peut être rompu, entraînant la dépassivation de l’acier et amorçant ainsi un processus de corrosion. Dans ces cas, la destruction du film passif et la dégradation du métal impliquent un mécanisme de piles électrochimiques comprenant des zones anodiques, des zones cathodiques et un milieu électrolytique constitué par la solution interstitielle du béton.
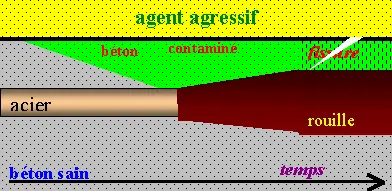
Au niveau de l’anode, le métal se dissout avec la production d’électrons, qui sont ensuite consommés au niveau de la cathode par la réduction de l’oxygène. Cette réaction libère des ions hydroxyle (OH-) qui réagissent ensuite avec les ions ferreux produits au niveau de l’anode, formant ainsi, en présence d’oxygène, des oxydes et hydroxydes de fer expansifs.
NOTE
Il est important de noter que la corrosion ne peut se produire qu’en présence d’oxygène. C’est pourquoi les cinétiques de corrosion dans les structures en béton immergé sont généralement très faibles. Ce processus complexe de corrosion dans le béton armé ou précontraint nécessite une attention particulière lors de la conception et de la construction des structures pour minimiser les risques de dégradation prématurée.
Quelles sont les causes de la corrosion des armatures dans le béton ?
Les causes de la corrosion des armatures dans le béton peuvent être attribuées à deux facteurs principaux :
- Carbonatation du béton d’enrobage : La carbonatation survient lorsque le CO2 atmosphérique réagit avec les hydrates présents dans la pâte de ciment, entraînant une diminution du pH aux alentours de 9. Cette baisse du pH entraîne la dépassivation des armatures lorsque le front de carbonatation atteint ces dernières.
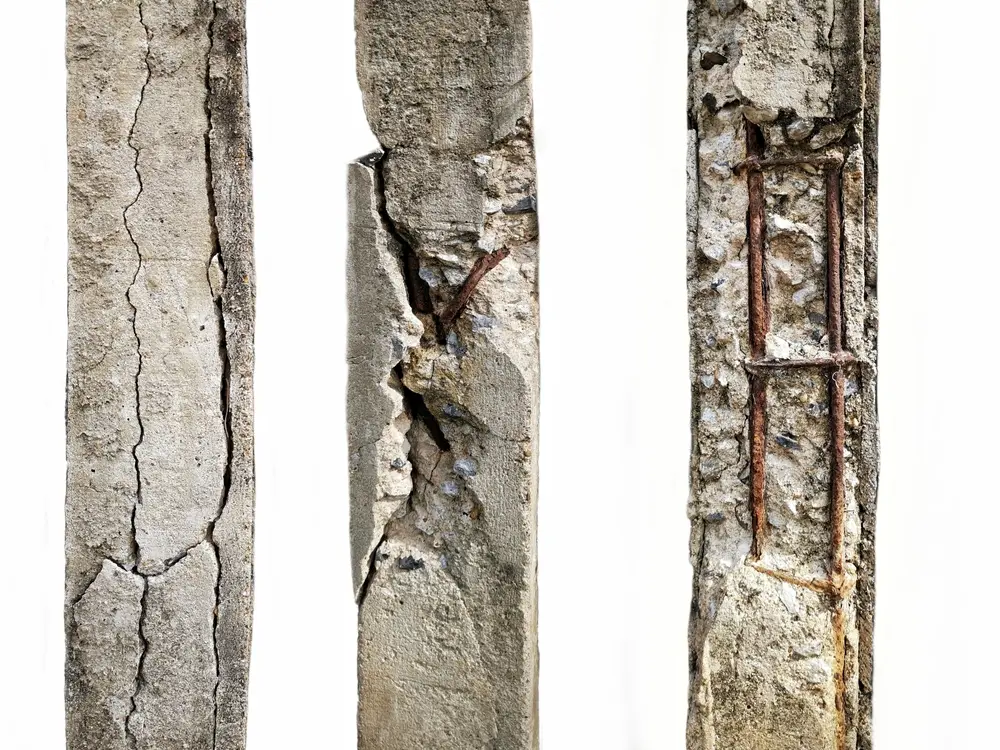
- Pénétration de chlorures : La corrosion peut également être initiée par la pénétration de chlorures provenant de l’environnement environnant, comme les milieux marins, l’utilisation de sels de déverglaçage ou certains milieux industriels. La dépassivation se produit lorsque la teneur en chlorures atteint un seuil critique au niveau des armatures. Ce seuil critique est généralement défini par un rapport de concentration Cl-/OH- compris entre 0,6 et 1, ce qui équivaut à une teneur en chlorures d’environ 0,4 % par rapport à la masse de ciment, comme stipulé par la norme NF EN 206-1 pour les bétons armés. Pour les bétons précontraints, ce seuil est abaissé à 0,1 %.
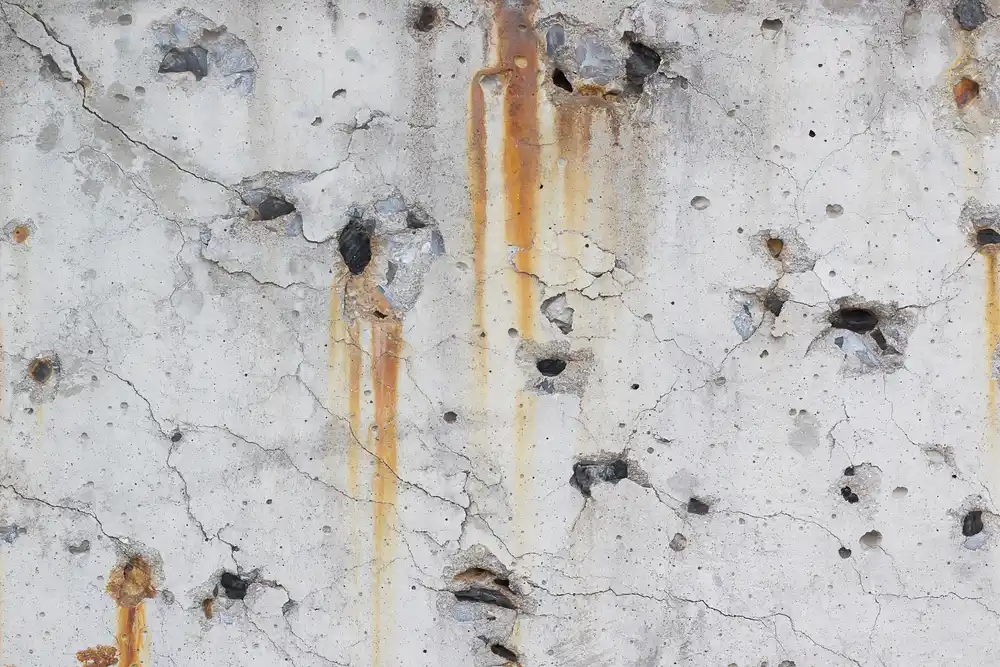
Quelles sont les conséquences de la corrosion des armatures dans le béton ?
La corrosion des armatures entraîne la formation d’oxydes et d’hydroxydes de fer, plus communément appelés rouille, aux dépens du métal d’origine, avec une augmentation significative de volume. Ce phénomène provoque une réduction de la section efficace des armatures, pouvant entraîner une diminution de la capacité portante des structures ou de leurs composants. Les premiers signes visibles de corrosion se manifestent souvent par des fissures le long des armatures, des décollements de la surface du béton, des coulées de rouille à la surface, et des éclats de béton.
Lorsque la corrosion est causée par la carbonatation du béton d’enrobage, les produits de corrosion s’accumulent autour des armatures. En revanche, lorsque la corrosion est initiée par la pénétration de chlorures, ces produits peuvent migrer à travers le système poreux du béton et apparaître à la surface sous forme de piqûres de corrosion.
Comment se prémunir contre la corrosion des armatures dans le béton ?
Lors de la phase de construction, la durabilité des bétons armés ou précontraints est étroitement liée à la qualité du béton et à l’épaisseur de l’enrobage autour des armatures.
Dans cette perspective, la nouvelle réglementation européenne établit, en fonction des classes d’expositions (risques de corrosion par carbonatation, chlorures marins, chlorures autres que marins), des spécifications précises concernant les paramètres de formulation des bétons et les épaisseurs minimales d’enrobage à appliquer (norme NF EN 1992-1-1 [Eurocode 2]).
Ces épaisseurs d’enrobage minimales, définies pour des bétons classiques avec des armatures en acier traditionnel, peuvent être ajustées, par exemple, lors de l’utilisation d’armatures en acier inoxydable ou lors de l’application d’une protection supplémentaire (comme un revêtement).
Les valeurs d’enrobage minimales sont plus élevées dans le cas des bétons précontraints, où les phénomènes de corrosion peuvent avoir des conséquences structurelles plus rapides et graves que dans le cas des bétons armés, où les dommages sont plus progressifs et prévisibles.
Que faire en cas de corrosion des armatures dans le béton ?
Avant toute intervention de réparation sur le béton affecté par la corrosion, il est primordial de réaliser un diagnostic approfondi afin de déterminer l’origine et l’étendue du phénomène de corrosion. Ignorer ce diagnostic pourrait conduire à des réparations inadaptées et peu durables.
Les étapes principales du diagnostic visent à :
- Cartographier les désordres visibles.
- Définir l’origine et l’intensité de la corrosion.
- Évaluer l’évolution des éventuels désordres, notamment dans les zones moins dégradées.
- Caractériser les bétons pour identifier d’éventuelles pathologies physico-chimiques associées et recommander des traitements de réparation adaptés, notamment en termes de choix du mélange granulaire pour contrer l’alcali-réaction.
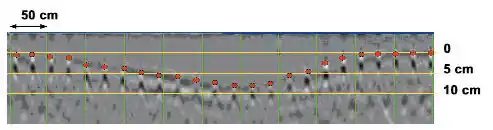
L’origine de la corrosion peut être déterminée en comparant les profondeurs de carbonatation (mesurées à l’aide d’une solution de phénolphtaléine) et de pénétration des chlorures (mesurées selon le protocole recommandé par l’AFPC-AFREM) aux valeurs d’enrobage. Pour les ouvrages exposés au milieu marin ou à l’utilisation de sels de déverglaçage, il est nécessaire de différencier les chlorures liés aux constituants du ciment des chlorures libres responsables de la corrosion par piqûre.
Ces relevés doivent être associés à des mesures d’activité de corrosion par potentiel d’électrodes et des mesures d’enrobage généralement effectuées par auscultation au ferroscan ou par radar.
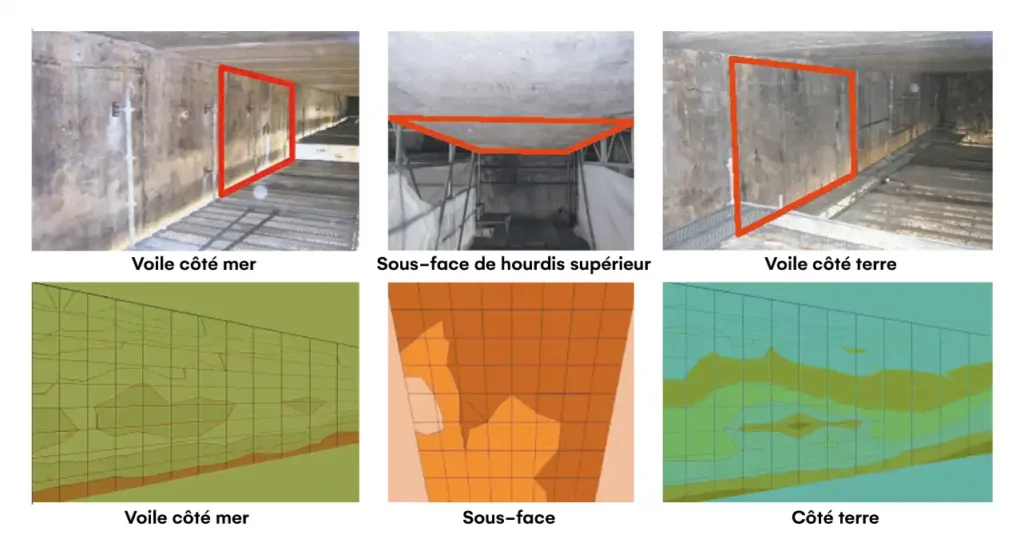
Ces différents essais fournissent les données essentielles pour établir un diagnostic de corrosion. Ils peuvent être complétés par des analyses physico-chimiques et microstructurales visant à caractériser les bétons en vue de recommandations de réparation appropriées. Dans le cas d’ouvrages peu dégradés, le diagnostic peut également permettre au maître d’ouvrage, grâce à l’utilisation de lois d’évolution et de modèles numériques spécifiques, de prévoir les risques de dégradation et de prendre des mesures préventives en amont, souvent moins coûteuses que les travaux de réparation ultérieurs.
Quels sont les différents types de traitements pour lutter contre la corrosion des armatures dans le béton ?
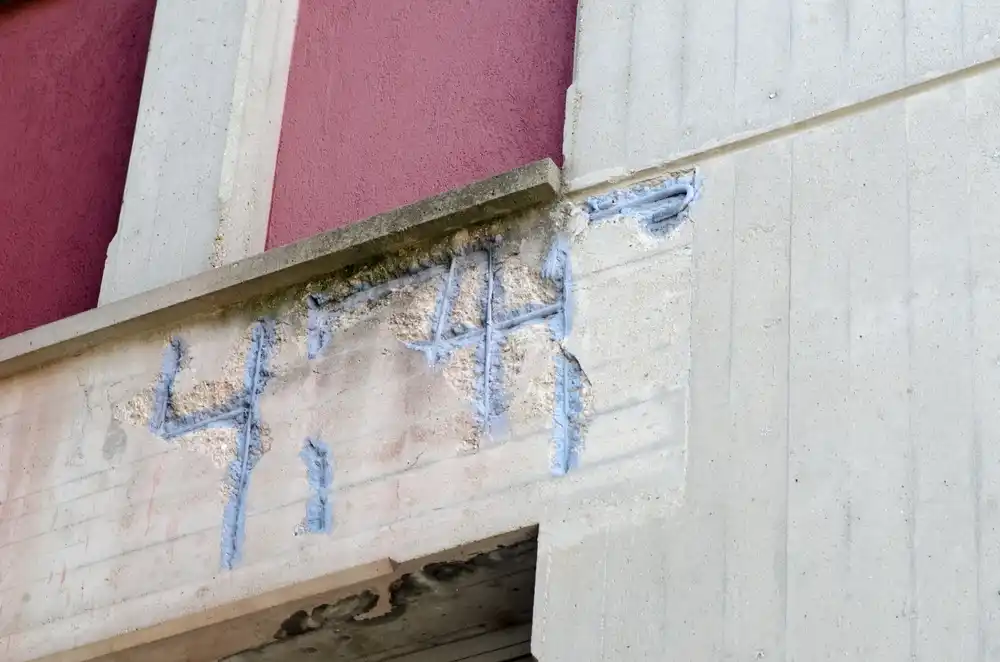
La réparation du béton affecté par la corrosion des armatures nécessite d’abord une purge des zones endommagées, étendue aux zones adjacentes, suivie d’un traitement des armatures. Ce traitement peut impliquer l’élimination des produits de corrosion et la passivation des armatures, ou leur remplacement en cas de diminution importante de section.
Pour des dommages ponctuels et sans risque de nouvelle corrosion à court terme, les zones purgées peuvent être réparées à l’aide de produits de réparation adaptés à la classe d’exposition de l’ouvrage, tels que des mortiers ou des bétons projetés.
En revanche, lorsque les dommages sont plus étendus et qu’un risque de corrosion future est élevé, plusieurs traitements préventifs et/ou curatifs sont disponibles :
- Traitements de surface : Ces traitements visent à protéger la surface du béton contre la pénétration des agents corrosifs. Ils comprennent les hydrofuges, les revêtements de surface (peintures, lasures), les enduits et les inhibiteurs de corrosion, qui ralentissent ou arrêtent le processus de corrosion au contact du métal.
- Traitements électrochimiques : Ils se divisent en deux catégories :
- Les procédés de réalcalinisation et/ou de déchloruration, qui visent à augmenter le pH de la solution interstitielle du béton autour des armatures et à extraire les ions chlorures présents.
- La protection cathodique, qui consiste à polariser les armatures en les utilisant comme cathodes, en abaissant leur potentiel électrochimique jusqu’à un niveau où la vitesse de corrosion devient négligeable.
En cas de dégradations sévères, un recalcul de la structure est nécessaire pour envisager d’éventuels renforcements structuraux.
Partagez cet article sur le réseau de votre choix :