5 principaux types de corrosion
La corrosion, ce phénomène insidieux qui ronge silencieusement les métaux, est un défi majeur dans de nombreux secteurs industriels. De la rouille qui dégrade lentement une surface métallique à la fissuration subite d’un composant sous contrainte, les effets de la corrosion peuvent être dévastateurs. Pour mieux comprendre et prévenir ce processus, il est essentiel d’explorer les différentes formes qu’elle peut prendre.
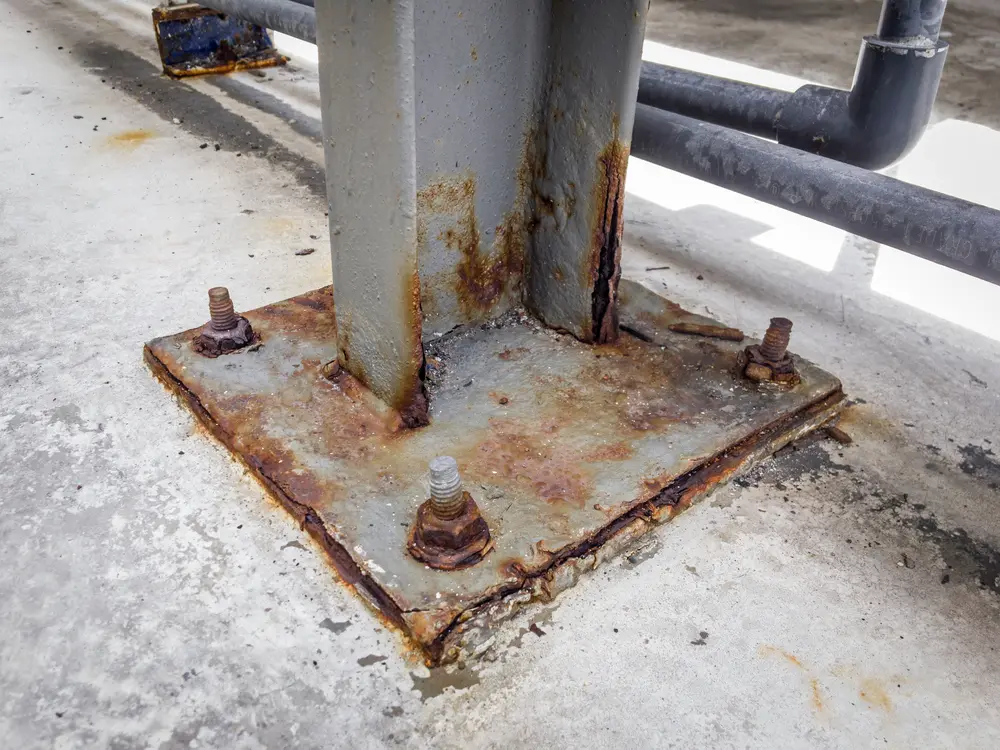
Dans cet article, nous examinerons en détail 5 types majeurs de corrosion : la corrosion uniforme, la corrosion par piqûres, la fissuration par corrosion sous contrainte, la corrosion en crevasse et la corrosion galvanique. En comprenant les mécanismes et les caractéristiques de chacune de ces formes de corrosion, nous serons mieux équipés pour protéger nos infrastructures et nos équipements contre leurs effets dévastateurs.
1. La corrosion uniforme
La corrosion uniforme est la forme la plus classique de corrosion et elle est relativement simple à repérer. Elle attaque une surface métallique de manière uniforme, causant l’apparition d’oxyde de fer, communément appelé rouille. Cette corrosion peut être mesurée en termes de diminution d’épaisseur par an (μm/an), ce qui permet de calculer l’espérance de vie d’un composant métallique.
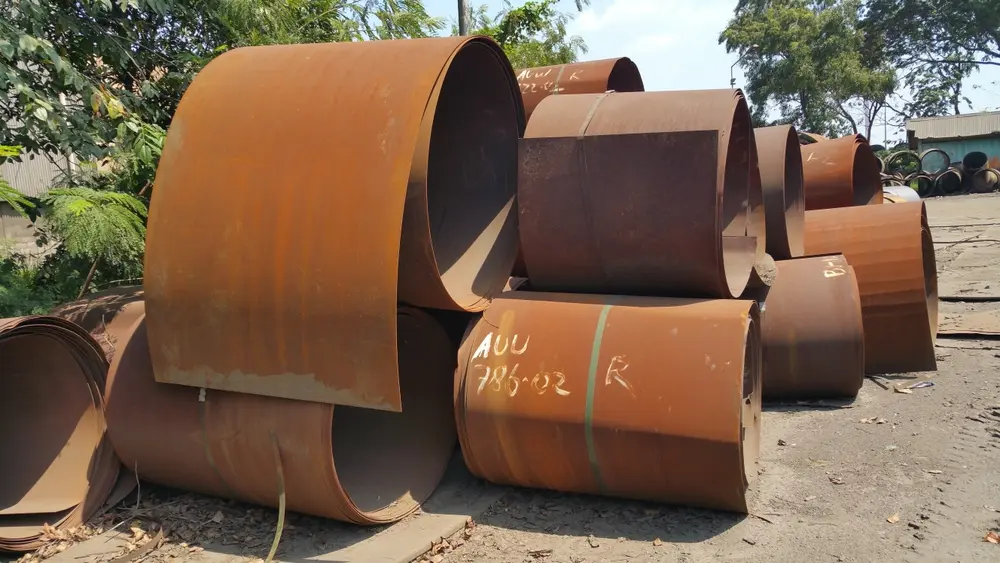
La corrosion par piqûres représente une forme localisée de corrosion qui engendre la formation de petites cavités à la surface d’un matériau. Ce processus corrosif se déclenche lorsque la couche passive, qui agit comme une barrière protectrice, se dégrade de manière localisée. Les cavités ainsi formées peuvent s’approfondir rapidement, alors que le reste de la surface du matériau demeure relativement intact. Les métaux et alliages passifs, tels que l’aluminium, le titane et les aciers inoxydables, sont particulièrement sujets à ce type de corrosion dès lors que la fine couche d’oxyde qui les recouvre localement est altérée.

La manifestation la plus courante de cette forme de corrosion se produit dans des environnements fortement agressifs, caractérisés par des températures élevées et une concentration élevée d’ions chlorure, comme on peut les trouver dans les piscines intérieures par exemple. Contrairement à la corrosion uniforme, la corrosion par piqûres est plus difficile à détecter, car les cavités formées sont généralement de taille minuscule, parfois à peine plus larges qu’une tête d’épingle.
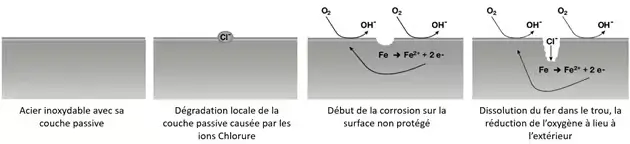
De plus, la quantité de matériau perdue en profondeur est souvent difficile à évaluer, ce qui rend la prédiction de la durée de vie de la pièce affectée ardue. Il est donc essentiel de prendre en compte les mesures de protection adaptées dès la phase de conception afin de prévenir efficacement ce phénomène.
3. La fissuration par corrosion sous contrainte (SCC)
La fissuration par corrosion sous contrainte (SCC), également connue sous le nom de Stress Corrosion Cracking, est une forme de corrosion qui résulte de l’interaction entre une contrainte de traction et un environnement corrosif. Ce phénomène peut entraîner la défaillance soudaine d’un matériau ductile soumis à une contrainte inférieure à sa limite élastique. Une petite cavité à la surface du matériau peut suffire à initier la formation d’une fissure, amplifiée par le niveau de contrainte présent dans la matière, qu’il soit résiduel ou appliqué. Les contraintes sont maximales au niveau du front de fissure, favorisant ainsi sa propagation.
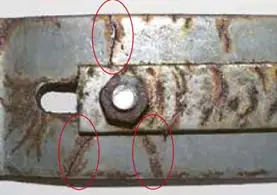
Une fois formée, la fissure devient auto-accélérée, car de nouvelles zones actives, non protégées contre la corrosion, émergent le long de celle-ci. Ces zones sont alors sujettes à la corrosion, fragilisant davantage le matériau et favorisant la propagation de la fissure. Ce processus se poursuit jusqu’à ce que la fissure se propage continuellement, entraînant une corrosion rapide du matériau à l’intérieur de celle-ci et conduisant éventuellement à une défaillance mécanique. Ce phénomène est particulièrement préoccupant, car même avec une contrainte bien inférieure à la limite élastique, le composant peut se rompre.
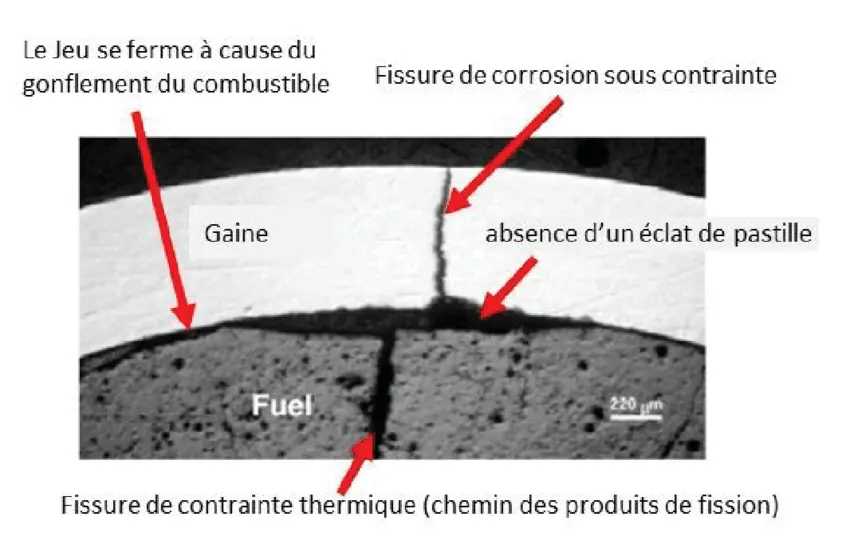
La SCC se manifeste généralement dans des alliages métalliques, notamment certains types d’aciers inoxydables, lorsqu’ils sont exposés à des environnements considérés comme « agressifs », tels que les piscines intérieures présentant une forte concentration de chlorure. Dans de telles situations, il est important d’utiliser des nuances d’acier inoxydable résistant à la corrosion, comportant notamment une teneur en molybdène supérieure à 6%. Il est donc essentiel de prévoir dès la conception la protection anti-corrosion adaptée à l’environnement d’utilisation, tout en minimisant les contraintes appliquées sur le matériau.
4. La corrosion en crevasse
La corrosion en crevasse, également connue sous le nom de corrosion caverneuse, est une forme de corrosion localisée qui se produit au niveau des espaces confinés entre deux ou plusieurs surfaces métalliques assemblées. Il s’agit essentiellement d’une variante de la corrosion par piqûres, se développant spécifiquement dans les zones à faible flux, telles que les recoins et les interstices où la circulation de solution est limitée. Cette forme d’attaque corrosive est souvent associée à la présence de faibles volumes de liquide stagnant, provoqués notamment par des cavités sous les têtes de boulons et de rivets.
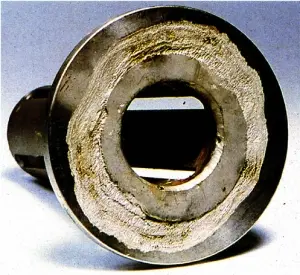
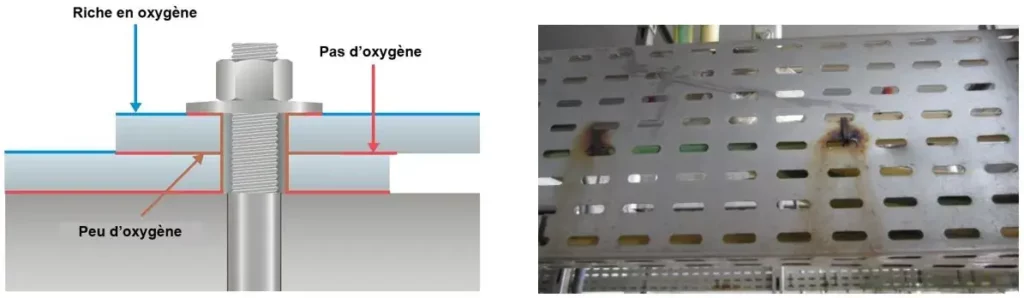
La dégradation du matériau survient principalement en raison des différences de concentration des constituants, notamment de l’oxygène, entre les surfaces impliquées. Dans une crevasse où la concentration d’oxygène est réduite, cette zone devient l’anode, favorisant ainsi la dissolution du métal et la progression de la corrosion.
En raison de sa nature hautement localisée, la corrosion en crevasse peut se développer de manière extrêmement rapide et parfois difficile à détecter. Cela représente un danger potentiel qui peut cependant être prévenu en choisissant judicieusement les matériaux dès la phase de conception, en adaptant les méthodes d’assemblage (comme privilégier la soudure) et en concevant des configurations moins sujettes à la formation de crevasses.
En mettant en œuvre ces mesures préventives dès le stade de la conception, il est possible de réduire significativement les risques associés à la corrosion en crevasse et ainsi assurer la durabilité et la fiabilité des structures métalliques.
5. La corrosion galvanique
La corrosion galvanique survient lorsque deux métaux différents entrent en contact ou sont connectés par un chemin conducteur électriquement. Dans ce processus, le métal moins résistant à la corrosion, souvent désigné comme le métal « moins noble », agit comme l’anode et se corrode plus rapidement. En revanche, le métal plus résistant à la corrosion, considéré comme le métal « plus noble », devient la cathode et voit son processus de corrosion ralenti. Cette forme de corrosion ne conduit à la dégradation que d’un seul des métaux en contact, le métal plus noble étant protégé.
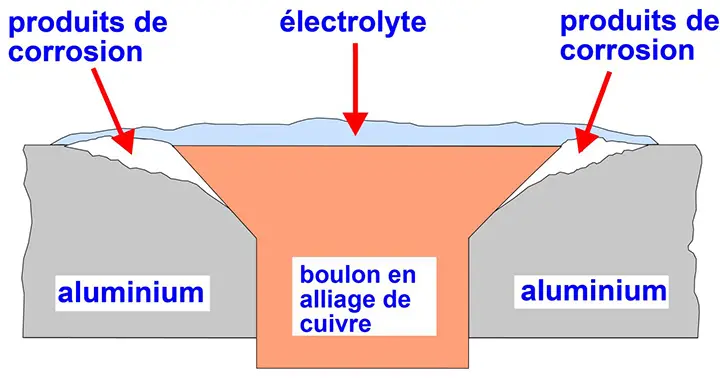
Ce phénomène, connu sous le nom de protection cathodique, est parfois utilisé délibérément pour protéger certains éléments métalliques en sacrifiant d’autres. Cette méthode est notamment employée pour préserver des structures métalliques enterrées ou immergées, telles que les coques de bateau, en favorisant la corrosion du métal moins résistant tout en préservant celui qui est plus noble.
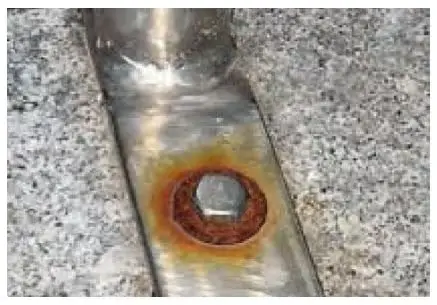
L’incidence de la corrosion galvanique sur la durée de vie des matériaux varie en fonction des métaux impliqués. Voici un tableau illustrant les effets de cette forme de corrosion pour différentes combinaisons de matériaux dans des conditions atmosphériques extérieures.
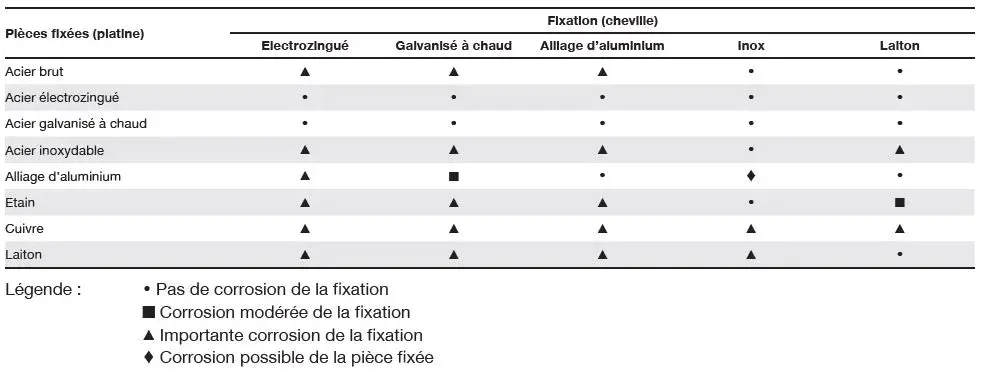
Conclusion
Partagez cet article sur le réseau de votre choix : & n'hésitez pas à laisser un commentaire :